Take the inline check valve for instance, this form of check valves has distinct advantages in certain applications, yet also has a few disadvantages. These disadvantages may be more apparent in certain applications. So in order to ensure that an inline check valve is the right choice for you and your application, consult with a trusted inline check value manufacturer who can provide you with the best possible product based on your needs and requirements. Read More…
Our check valves are manufactured with the customer in mind. We believe in offering superior products and services every time. No matter whether you are looking for small or large valves, we can meet your every needs. It is our goal to offer excellent prices and service to each customer. Contact us to learn more today!
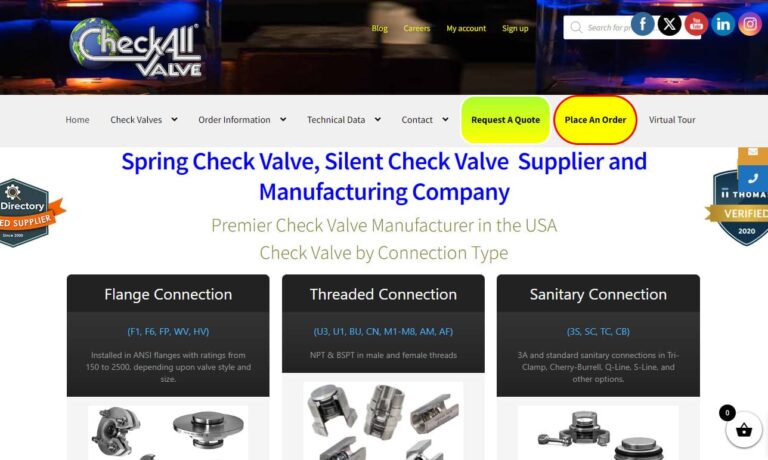
We are an ISO 9001:2000 and our customers know that with that they are receiving not but product s made out of the highest quality raw materials. We are capable of machining ball valves from 1/2 inch up to sixty inches in order to better serve you! All of our products are put through extensive testing to ensure that we are providing the best products possible. Get in touch with us today to learn...

At Red-White Valve Corp, we take pride in delivering premium-quality check valves designed to meet the highest performance and reliability standards. Our check valves are essential for controlling one-way flow and preventing backflow in a wide range of applications, ensuring the efficiency and safety of fluid systems. With decades of experience, we have developed a comprehensive line of check...

At Kepner Products Company, we specialize in designing and manufacturing high-quality check valves that deliver reliable performance across a wide range of applications. Our valves are engineered to provide precise control of flow and pressure, ensuring optimal system efficiency and safety.

More Inline Check Valve Manufacturers
Lift check valves are installed in the pipelines of various industrial facilities as well as commercial and residential plumbing. Industries such as water treatment, medical, food and chemical processing, petrochemical and agriculture use this particular type of pump to normalize the unidirectional flow of various materials such as water, chemical vapors, air, steam and more.
Boilers, mixers, faucets and metering pumps employ this type of non return valve. When installed, a disc or cone-like plug rests on the seat or passageway in the cross section of the valve, blocking the flow of materials. When fluid or gas flows at the optimal pressure or higher in the pre-determined acceptable direction, it pushes the disc away from the seat.
As the disc, also known as a lift, slides along an attached rod located on the downstream side of the check valve, it creates a gap through which the process stream may flow. When this forward flowing pressure drops and downstream pressure reaches the valve, the disc or cone is quickly pressed back into place. A tight seal is created that prevents backwash.
The design or configuration of a lift check valve is similar to that of a globe valve. The body is a semi-spherical or cylindrical device that is installed mid-stream into a pre-existing pipeline. An internal baffle divides this compartment into two halves. At the center is the valve seat, or opening, into which the aforementioned disc or cone-like plug can be placed to form a seal. This stopper is attached to a dowel, which in turn is attached to the downstream wall of the sphere or cylinder.
Known as a stem, this is a cold rolled or extruded rod along which the disc slides as it encounters pressure from the process stream. The cylinder, seat and disc of a lift valve are most commonly made of durable metals such as aluminum, stainless steel, brass and iron. Despite their popularity, these materials can be used only in applications where slight leaks may be permitted. However, plastic and elastomeric components can compress and create a tighter seal that will eliminate the risk of potentially harmful leaks.
It is important to consider the process stream and the chemical compatibility of these materials when selecting the proper valve. While traditional lift check valves are more common, piston lift valves offer a slight modification. Instead of a cone shaped disc, a piston shaped plug is used with a dashpot, providing damping during operation.
The use of a dashpot reduces valve wear, which thereby increases product longevity. Although both traditional and piston lift check valves are often bulkier than alternatives such as wafer check valves and swing check valves, it is a robust device that is suitable for installation in both horizontal and vertical lines with upward flow.